“Replicating” the Future of 3D Printing
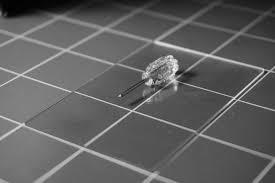
COURTESY OF STEPHEN MCNALLY The handle of this screwdriver was printed around the metal using “The Replicator” 3D printer.
Although it’s far from the futuristic version shown in Star Trek, “The Replicator” 3D printer, developed by researchers at UC Berkeley and the Lawrence Livermore National Laboratory, is a major advancement in the 3D printing industry. This printer uses light to sculpt structures out of liquid resin instead of the plastic layer-by-layer approach used by most 3D printers today.
According to The Daily Californian, researchers Brett Kelly, Indrasen Bhattacharya, Hossein Heidari, Maxim Shusteff, Christopher Spadaccini, and Hayden Taylor developed “The Replicator” 3D printer, which can “create solid materials all at once, as opposed to layer by layer, using light.” Hossein Heidari told The Daily Californian that they named their printer “The Replicator” after a machine used in Star Trek that could print objects out of thin air. The real-life “Replicator” creates detailed 3D shapes and components by projecting images onto a rotating container filled with a gooey, light-sensitive liquid. Based on footage produced by Mashable, structures and objects emerge from the liquid in under two minutes.
The process, called Computed Axial Lithography (CAL), avoids some of the drawbacks of traditional 3D printing. According to the researchers of the project in Science Magazine, images of a 3D object are turned into a video sequence that shows the object from every angle. A projector projects the images onto a rotating container filled with a light-sensitive polymer called resin. Areas which receive more intense light solidify as the container turns. The remaining liquid polymer is then drained, leaving a solid 3D replica of the image that was projected. The unused liquid can then be recycled for the same purpose, making the process 100% renewable. As for the projector, any off-the-shelf projector can be used, according to Hayden Taylor, the senior writer of the article. Don’t be fooled by its simplicity, though. According to Taylor, “there are a lot of subtleties to it—how you formulate the resin, and, above all, how you compute the images that are going to be projected, but the barrier to creating a very simple version of this tool is not that high.”
To the naked eye, the process makes it look like the object being printed is being pulled out of liquid nothingness. This process eliminates the discrepancies in design that many traditional 3D printing machines encounter when producing objects. The current 3D printing process involves superheating a plastic filament and then creating the object by layering the filament one layer at a time to slowly create an object. If a structure has overhangs, it requires support material to be printed, as it can’t be printed in mid-air. Comparatively, the solid object formed by CAL is smooth and does not need support structures, meaning there is less wasted material. Additionally, the current layer-by-layer process produces a rough feel and staircase-like appearance of the object, which is not the case with the CAL.
Though it is compelling, this new 3D printing process is still a new development, and it will have to be refined before it can be made available to the public. However, this development could be the next step in structural engineering design, and may further the effect 3D printing has already had in the scientific world.